Case History 2: A Successful Peer-to-Peer PM Group Led a Company Adoption of Lean
By Dan Fauchier
Fifth in the Series
For over two years, a group of roughly ten Project Managers, Assistants, a Superintendent, and a Pre-Construction Manager in the Boston area have participated actively in a monthly Video Action Team, taking turns facilitating. Their company, Mill Creek Residential (MCR) specializes in the investment, development, construction, acquisition, and operation of rental communities. Since their founding in 2011, they have raised approximately $4 billion of equity in fund-like structures and deployed $17.8 billion in capital to acquire land, design single-family built-to-rent and multifamily structures, manage the construction with full-time leadership, and ultimately lease rental homes long-term.
Mill Creek commenced the pilot of the Last Planner System® (LPS) in 2019 to improve project outcomes, including schedule reliability. By 2021, they organized the Video Action Team in Boston “to better prepare our project teams prior to project start and initial LPS kick-off training so that when the kick-off training was rolled out at their projects, the teams would be better prepared and have a better understanding of the LPS and the expectations of the team in implementing the use of the LPS as a part of the project management process.”
Monthly, the Video Action Team (VAT) began watching Construction Accelerator® Last Planner videos and then discussing them using the VAT Guides that Construction Accelerator® provides as part of their Enterprise subscription.
After a session on “Roles in LPS®” these insights were offered by participants:
- Doing a Phase Pull forces the foremen to think through the work. When we give them a schedule they don’t necessarily do that. Push leads to reactionary state and vice versa.
- When you start the Pull process, it has compounding benefits; foremen see they have input, don’t have to work OT, see the flow, and have ownership.
- LPS gives creditability and reliability to those outside the construction process and reporting through the organization. Also improves morale and communication.
- We’re pricing a lot of projects with trade contractors now, and instead of asking, “Who’s the Super?” it’s “Oh, you’re running this like Modera Framingham by Mill Creek (lean LPS).” Trades feel like they are part of the process, and their price improves. A lot needs to go into even weekly meetings; we weren’t as prepared on past projects.
- Backlog, incorporating materials supply problems, good discussion on adapting pull plan to world changes.
- Phasing, I’ve been emphasizing our 6-week; yesterday, I had a breakthrough with some guys for 90 minutes in the “middle tier” phase plan to get the entire finish sequencing on the board.
- The theme is “change.” Modera Framingham was different from Modera Marshfield and different from the ones we’re doing now; the future is more about logistics.
- When we started doing Daily Huddles our PPC went from 70% to 90%. Creating the boards and seeing them daily on the jobsite (during Covid). And in another site, trailers were a couple of blocks away, out of sight, out of mind. Daily Huddles are “trust but verify”. Weekly meetings get easier. Stress levels go down, too.
This peer-to-peer learning – coupled with in-the-field expert coaching for new projects around the country – became so powerful and effective that in 2022, four executives of the construction division formed a Lean Working Committee and by 2023 had surveyed 40 US projects to measure LPS effectiveness and field leadership attitudes, formed a group of 40 Lean Champions led by 4 of the most experienced Champions plus the Construction Divisions Senior VP, developed with their SVP of National Training to bring MCR Company-Wide Enterprise Account into their Workday system and achieved 100% participation and completion of required video modules and 60% participation of the optional videos.
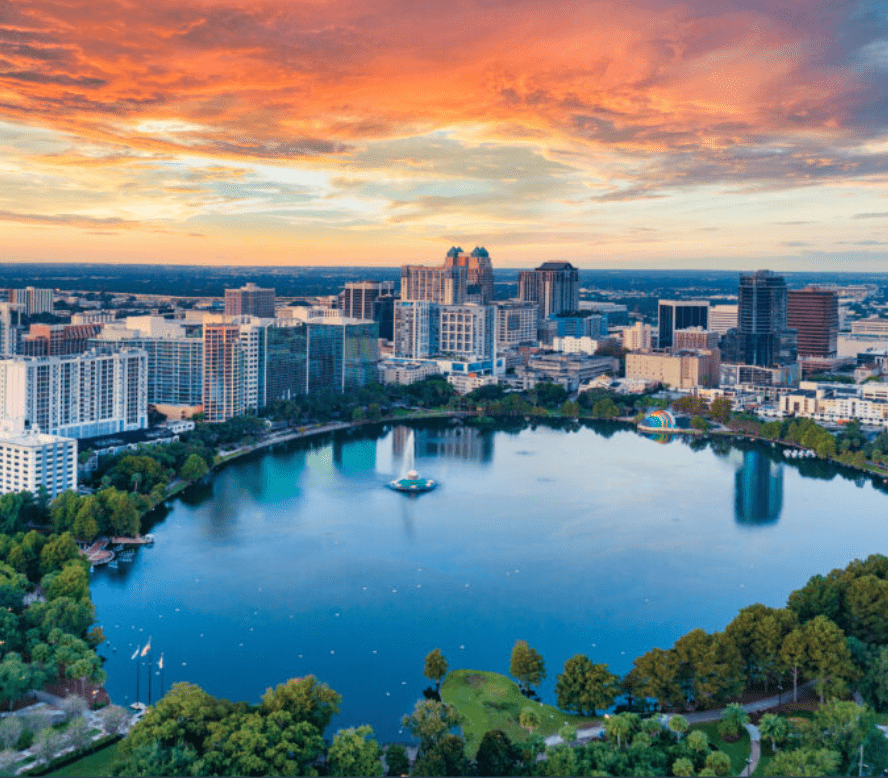
Having laid the groundwork for this company-wide adoption, the original VAT peer-to-peer group continues meeting and has moved into related Lean topics, including 5S, Root Cause Analysis, and Process Mapping, which included the whole group remapping the process for issuing subcontracts on a project. Next, they are tackling “The Visual Workplace”.
Reflecting on the overall Video Action Team process, team members offered these evaluations:
- These VAT meetings are interesting because field team members have already done LPS, then we compare our experience to the videos, plus between jobs keeps us sharp, talking about it every few weeks.
- When we get to our projects, we’ve got to be in a position to lead Last Planner right out of the gate with our subs, and the more familiar we are, the better leaders we are when we are challenged. It gives us more confidence, and we can teach others.
- We had some discussions before gaining access to the CA system. The CA videos really help. Group sessions bring our thoughts together by the end of the session.
- It helps us as a team really learn the material. We’ve practiced it, so videos have brought us together as a team. Also, we were doing it, but doing it wrong in many cases. This is definitely helping.
For more on Video Action Teams: https://constructionaccelerator.com/video-action-teams